Lots done over the weekend. Assembled the engine, and did a pressure test. First off another nod to ToraTora, when assembling I coated the paper gaskets with engine building lube. Super sticky stuff that keeps the gasket from ripping if, or when, you need to open things up again.
With everything buttoned up, I could finally check the squish. Simple process is to use a bit of solder, couple of inches worth. Bent it gently so you can stick it down the spark plug hole and point it towards the side of the cylinder. Craig the engine over, and you will feel the piston as it touches the solder. Keep cranking, and the piston will smash the solder against the head. Now you have a good idea of how close the piston is getting to the head.
Our target was between 0.85, and 0.75 millimeters. We can go back later and change out the base casket to make subtle changes is the final squish. The setup we are going to start with are:
0.85 mm squish at the piston edge
0.95 mm squish at the inner edge of the squish band
0.65 mm base gasket
It's a rather thick base gasket. But has the benefit of raising the cylinder putting the bottom of the ports, at the top edge of the cylinder at BDC.
With that settled, it was on to pressure testing. A simple process, using some rubber compression plugs. I only took the pressure it to 5lb but everything looks good. If you do this, you will see the pressure dropping if you only look at the gage. So grab some bubble soap and start smearing it around the gaskets. If you have a leak, you will se large bubbles forming. You can confirm that the leak is in the rubber plug shaft by smearing that as well.
One other thing to note. With the Airsal Extreme kit, the exhaust studs go into the side exhaust ports. So use some high temperature coper gasket compound to help seal the threads.
With the engine in a good state, it was on to keys and locks. The bike came with one key that fit the ignition lock, and the fake tanks lock. But didn't fit the pilot seat. So it was off to find out if the lock could be re keyed. Or if I would need to find a 3 lock set. Turns out it's not that hard to re key one of our locks. This link will do a better job than me of describing the process. (
https://electricmotorcycleforum.com/boa ... pic=9330.0)
My lathe is a small hobby tipe. So cross cutting can sometimes push the cross slide backwards. So I use a clamp to keep that from happening.
Nicely cut down, and polished up
And don't forget to cut the gasket to match the cylinder
All ready to be buttoned up

You can see how the stud hole goes into the exhaust side port
[url=https://flic.kr/p/2nuHzA3]
All buttoned up with a little bit of pressure
And some bubbles through the center shaft of the rubber plug.
It's simple to make on of these. Just grab 2 rubber plugs from your hardware store. Find a car cylinder pressure tester at a swap meet, or yard sale. And order a blood pressure cuff. The gage goes to 300 mmHg (millimeter of mercury). That's about 5.8 PSI. You don't want to go over 7PSI as you may blow out a seal. Not as big a deal in a single cylinder engine. But on multi cylinders you risk blowing out the center seal. And that means you get the opportunity to rebuild the engine again.
And lastly some pick of the lock, and it's re-key
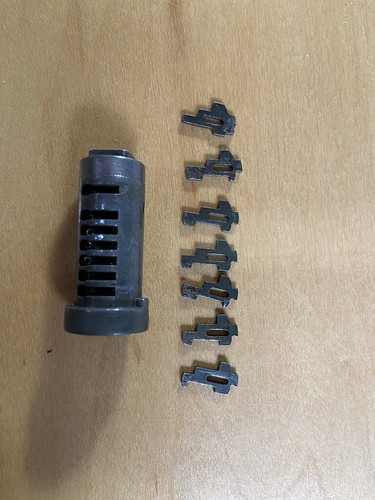